How to effectively carry out a ‘Finite Element Method calculation’.
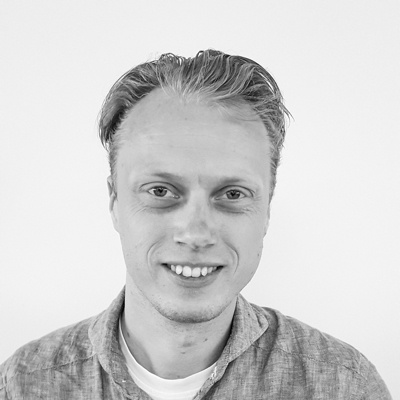
In order to test what is the influence of the forces that are exerted on products, you can use ‘Finite Element Method calculations’. This way, many optimizations of the product that is being developed, can be carried out before the actual development of a prototype. Provided that it is carried out accurately and efficiently, the FEM calculation reduces costs and also creates a faster run time.
What is a Finite Element Method calculation?
A Finite Element Method (FEM) calculation is a calculation method that makes it possible to simulate physical stress on parts of a model to see if it is sufficiently strong and rigid. Other problems can also be simulated by means of a FEM calculation, such as flow, heat transfer, vibrations, thermal stress and crash or fall simulations.
The calculation that is carried out on a digital 3D model is always an approximation of reality. The calculation is therefore validated and verified later by exerting the same forces on a prototype.
Using FEM calculations
FEM calculations are predominantly used to test critical components that are placed under extreme pressure. By carrying out these calculations it becomes more efficient to implement optimizations. When we know where to locate any possible problems, we can solve them before a prototype is developed. This way, the number of prototypes that need to be developed is reduced and so are total run time and costs.
How are FEM calculations carried out efficiently?
To be able to carry out a FEM calculation efficiently, it must be done in three stages:
- Pre-processing;
- Processing;
- Post-processing.
Pre-processing
During this stage we determine what we would like to research. We will also define the desired results of the calculation. It is important that the 3D model is simplified so that only the most essential details are incorporated in the calculation. If we do not do this, a calculation will take more time than needed.
In addition to that we also need to study which forces affect your model and how this happens. It is important to find a way that is as realistic is possible, so that the results we get from the calculation are actually useful. One good way is drawing a Free Body Diagram. This is a graphical means to reveal and analyse which outside forces affect the model.
All this power data and that materials that are used are processed together in the software that the calculation is going to carry out. Post en Dekker use SimScale for this.
Processing
During the processing stage the calculations take place. It is important that several stress scenarios are calculated in order to get a realistic result.
Post-processing
Now the FEM calculation has been completed we will start with the analysis of the design. Check whether the results are realistic and whether there are any unexpected factors. We could also do a manual calculation to verify the results.
All results are recorded in a report. This includes:
- How the calculation has been set up;
- What has been calculated;
- What the preconditions are;
- What the outcome is.
After this, the design is optimized and new FEM calculations are carried out, if necessary. When the design has been approved, a prototype can be developed. This prototype will later be put under stress in the same way as to verify all calculations.
Carrying out FEM calculations is an effective method to decrease costs and run time. Do you need more information or are you looking for support? Then please contact us.