The product road map, the basis of integrally designing of product families
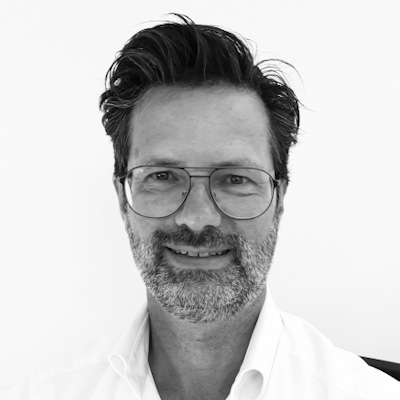
An integrally designed product family is optimally matched to market requirements, business processes and the supply chain. It is a product family that has been developed measurably efficiently and effectively and can be generated and controlled.
Starting point for an integral design, is the product road map. In this article I will explain what this looks like.
The roadmap has several fixed stages:
Market research and technological identification
During market research or customer-value analysis, opportunities for a new product (and/or platform or system) that complies with certain unique user specs, are inventoried. Following that, the technology that should make the most promising product possible, is identified; the user specs shall be translated into functional specs. Specification goes according to the V-model.
Risk analysis and concept to detail engineering
The roadmap aims to eliminate the risks and increase acceptation with stakeholders. Technical risks are identified and developed in sprints into proof of concepts.
For concept, basic and detail engineering, we can draw from an extensive set of designs that should make the development process run efficiently and effectively. Examples of this are 3D printing and testing of concepts in an early stage, digital product analyses and simulations.
The development chain is organised, future partners from the supply chain are involved at the right moment to optimally tailor the design to the production opportunities.
Translating research
The results of the research are translated into a new technology platform and/or module, that focuses on a specific market and application. On this platform, a modular system architecture can be defined. This architecture with functional modules is translated into a product structure with physical modules. This modular structure is implemented into a product configurator, with which customer orders can be generated.
Defining of modules
The crux of a flexible product platform is to cleverly define the modules from which a family is built up. Therefore, a MFD analysis (modular function deployment) is carried out. This starts in the innovation roadmap with a QFD analysis (quality function deployment) to obtain the user and design requirements, with a focus on modularity. On that basis, possible technical solutions and accompanying modular concepts are selected. Where useful, several functions can be integrated into one module, not neglecting the fact that it is logical to keep customer-specific and generic modules separated.
The generated functions will be assessed by means of the so-called ‘module drivers’. In all, there are twelve module drivers that are, according to the Treacey & Wiersma model, divided into Operational Excellence drivers (OE, 5 units), Product Leadership drivers (PL, 4 units) and Customer Intimacy drivers (CI, 3 units). From the analysis it should become clear how the functions can be combined into modules. Depending on the strategic orientation of the OEM developer in questions, a preferred selection of modules comes out.